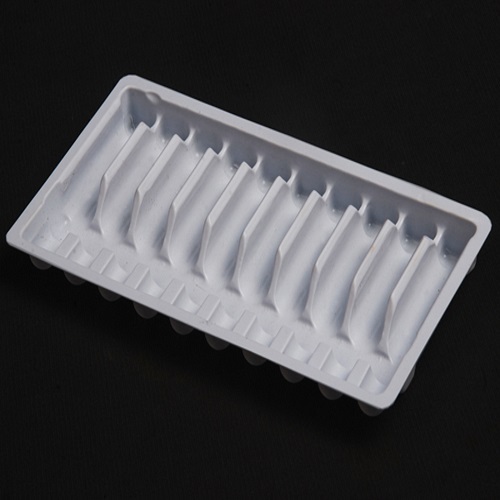
Plug forming is a thermoforming procedure that uses a plug or male mold to press the heated thermoplastic material into the female mold prior to the application of a vacuum. This method helps uniformly distribute the sheet.
Depending on the surface area of the parts being manufactured and the dimensions of the clamp frame, tooling for injection molding can cost two to three times more than the amount for tooling for plastic thermoforming or vacuum forming.
In addition, while vacuum forming is often the most cost-effective choice for small to mid-range production quantities, other plastic manufacturing processes can be more affordable for very large production runs.
Vertical farming, hailed as the "future of farming", needs a whole new set of skills never before seen in agriculture. What's behind the hype?
We have extensive experience of delivering cost-effective press formed parts and products. With a skilled and experienced team supported by large capacity and efficient machinery, we can produce complex, large or multi-part items cost-effectively and with fast turnaround if required due to our flexible working processes.
We offer unbeatable insight into this complex process to ensure we deliver the best quality products and parts at the best possible price. As well as some of the most efficient plant available we also have dedicated teams designed to support your project – from designers to operatives, project managers to logistics we can offer an end-to-end service for large or small projects.
LMC’s CNC machines use robotic technology to quickly finish products in the tight tolerances that our customers require.
The actual vacuum is applied at this step. After pre-stretching the materials, a vacuum is applied to aid in the formation of the sheet. The air trapped in between the mold and the plastic sheet is removed by a vacuum pump.
Ashford Orthodontics, the largest specialized orthodontic laboratory in the UK, is pioneering dental appliance manufacturing using a blend of 3D printing and vacuum forming.
In this article we briefly look at the characteristics of the six most popular thermoplastics that we use in our vacuum forming processes
Experienced production staff, a dedicated design and CAD team and the very latest software and machinery ensure we can fabricate to the very highest standard.
You can unsubscribe whenever you want. We won't bother you, promise. To learn more about our data protection policy, click here
So you want to live in Brazil despite the recent political conflict? We salute your courage! Here’s the lowdown if you’re looking to relocate to the legendary city of Rio Clique neste link do Janeiro.
LMC’s forming and production areas have a wide range of capabilities. Draw depths can range from parts of an inch, all the way up to 3 feet.